It's been a while since we posted to the Rat-Hole blog so I though I'd share some photos.
Here is the messy room before we cleaned it up (for my brother's visit on Halloween).
Some detail shots of painted trim, crown moulding, and curtain rods (no curtains).
The chronicle of the trials, tribulations, and joys of attempting to update a 1930's-era home, affectionately termed "the rat hole" because of its state of disrepair, in Kenmore, Washington.
Monday, November 24, 2008
Wednesday, October 08, 2008
Nice and Trim
So while my brother and I were working on getting the outside painted in preparation for inspection (that man worked like crazy while I did my day job - we couldn't have met our permit deadline without him), my spouse was working like crazy on the inside trim. He did a beautiful job, and we think the windows turned out really nicely. We're especially happy with the way the sill turned out.
Now that our permit's complete, we're doing a couple of side projects to prep for the next round of ripping out the den. Right now my spouse has been working on building a cabinet for our tools, so we don't have to keep moving them around the rooms as we work on them anymore.
I'll post more pictures when the cabinet's complete, because I think it looks good and will be really useful (especially since we can't build our shed yet).
Next up, while the spouse works on the drawings for the next permit, my brother and I will paint the interior window trim (white) and measure/install/paint the crown moulding. Then it's time for the bookshelf, and hopefully we'll have that all in by Thanksgiving, so we can rip out the den in early December.
Now that our permit's complete, we're doing a couple of side projects to prep for the next round of ripping out the den. Right now my spouse has been working on building a cabinet for our tools, so we don't have to keep moving them around the rooms as we work on them anymore.
I'll post more pictures when the cabinet's complete, because I think it looks good and will be really useful (especially since we can't build our shed yet).
Next up, while the spouse works on the drawings for the next permit, my brother and I will paint the interior window trim (white) and measure/install/paint the crown moulding. Then it's time for the bookshelf, and hopefully we'll have that all in by Thanksgiving, so we can rip out the den in early December.
Sunday, October 05, 2008
Siding Sojourn
As you know, we've passed our final inspection, and we're really, really pleased with the way everything looks. So, this time, we're going to go through and show the progression of the siding, from start to finished product. When we get the insides closer to finished (more moulding, trim painted) we'll do the same thing there.
Rear of the house (south wall):
Side of the house (east wall):
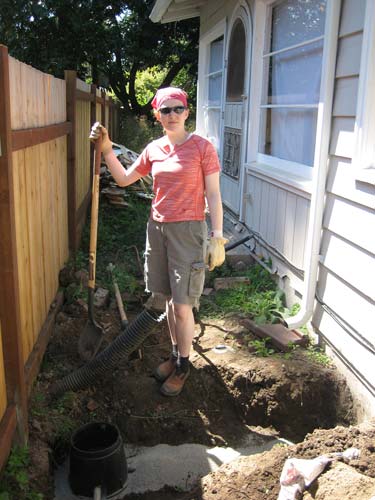










Rear of the house (south wall):
Side of the house (east wall):
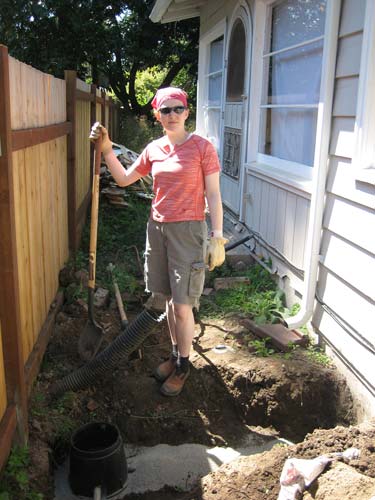







And here are a few details pictures that we liked:


Finally, the siding is finished, and we think it looks nice.

You can't really see the work we did on the siding unless you walk around the side of the house - it isn't visible from the road. Which is bad, because we think it looks so sharp, but it's also good because then our patchwork house doesn't look more "Frankenstein" than it does already.
We'll post more later this week!
We'll post more later this week!
Monday, September 29, 2008
FINAL INSPECTION: PASS!!!
Just a note to all of our loyal followers... we had a final inspection (for the dining/living room) at noon today and... WE PASSED!!!
We are pretty tired and sore. And definitely looking forward to a little break. But wait! How did we get here?
More later.
We are pretty tired and sore. And definitely looking forward to a little break. But wait! How did we get here?
More later.
Monday, September 22, 2008
Not Dead!
Just wanted to drop a quick note and update to let everyone know we're not dead.
We've been hot and heavy into the siding, which is nearly finished now, and the interior trim around the windows. It's been going mostly well. We've been working so hard that there hasn't been time to update the ol' blog, between rat hole work and job work.
The permit expires next Monday, so we'll continue to have our heads down this week. We have to finish the siding and exterior trim and paint it all, and do the window interior trim and paint that. It doesn't seem like much, but this sort of thing always takes longer than we expect it to, so we'll just be craking this next week and weekend. Try to send us good weather thoughts, heh heh.
I'll try to do a longer post with glorious photos soon.
In other news, my brother has successfully moved in and is totally rocking the rat hole. We're very glad to have him!
We've been hot and heavy into the siding, which is nearly finished now, and the interior trim around the windows. It's been going mostly well. We've been working so hard that there hasn't been time to update the ol' blog, between rat hole work and job work.
The permit expires next Monday, so we'll continue to have our heads down this week. We have to finish the siding and exterior trim and paint it all, and do the window interior trim and paint that. It doesn't seem like much, but this sort of thing always takes longer than we expect it to, so we'll just be craking this next week and weekend. Try to send us good weather thoughts, heh heh.
I'll try to do a longer post with glorious photos soon.
In other news, my brother has successfully moved in and is totally rocking the rat hole. We're very glad to have him!
Thursday, August 28, 2008
Deep Sh-t
There were so many good possible titles for this post we almost couldn't choose one.
Today we got our septic tank pumped. And found out that it probably won't last us another year, so we should try to get hooked up to the sewer before the end of winter. Maybe it will last until next summer. It's $7,000 just to get permission to hook up to the sewer, and it will take roughly $5,000 to pay someone to dig the trench, lay the line, and hook it up. So now it's a race against time to raise/save the money. FUN!
It's not like it's one of those things you can put off, either. I really like being able to flush my toilet.
So, let's start at the beginning of the septic saga.
The guy shows up with his truck. He and my spouse go around back and talk about where the tank is. The fella, being larger than we are, immediately finds it because he walks over it and it bends. Well, that was easy. Apparently neither of us who actually own the property have been big enough to feel the bending before. Well, that saves us some time and money trying to locate the thing. The guy tells my spouse that we need to put a sheet of plywood over it or something to keep someone larger than we are (read: my brother) from accidentally falling in.
Then, they open it up. Horrors. We've tried to protect the innocent, considering what you're looking at.
Turns out that our tank is probably an old Sears model from the 1950s, iron, about 500-600 gallons. It's been retrofitted, probably by the previous owner. Super. The guy tells us that if he was inspecting our property, and saw this setup, he would have never given it a pass. Good to know. Three years later.
(You can tell that this whole episode doesn't bother me at all. $12,000 or suffer toilet trauma like never before doesn't bug me at all.)
Anyway, the guy pumps it.
Nice and "clean." At this point in time he thinks that we could probably last on the system a couple more years.
Then he tests our leach field. Turns out it doesn't really leach. At all. For $500 cash (it usually costs $800-$1,000) he'll come out and try to make it drain better. No guarantees that it will work, of course. At this point, there's really not much more to do but seal the thing up.
After he leaves, my spouse calls the utility district. They confirm the prices, and then say that we can actually do all the work ourselves to save us that $5,000. But, we'll have to sign a waiver that we'll be liable and pay for any problems in the line "downstream" of us ourselves. I don't know about you, but that sounds like an awful lot of liability to me. So I'm not so comfortable with that, either, even though it saves us money. We could dig the trench ourselves, and have a contractor could lay the line and do the attachment. We'll have to price that out and see how it goes.
We should even be able to decommission it ourselves. That will involve getting an inspector over here, who will watch us get it pumped, break the bottom out with an iron tamping bar, and then fill it with sand. Then I might dance on top of it and light my money on fire, you know, just for fun.
At any rate, we need to do something. This isn't a problem that will just go away or solve itself. But we won't worry about it right now. My brother moves in with us this weekend. We'll just have to let him know to go easy on the tp.
Today we got our septic tank pumped. And found out that it probably won't last us another year, so we should try to get hooked up to the sewer before the end of winter. Maybe it will last until next summer. It's $7,000 just to get permission to hook up to the sewer, and it will take roughly $5,000 to pay someone to dig the trench, lay the line, and hook it up. So now it's a race against time to raise/save the money. FUN!
It's not like it's one of those things you can put off, either. I really like being able to flush my toilet.
So, let's start at the beginning of the septic saga.
The guy shows up with his truck. He and my spouse go around back and talk about where the tank is. The fella, being larger than we are, immediately finds it because he walks over it and it bends. Well, that was easy. Apparently neither of us who actually own the property have been big enough to feel the bending before. Well, that saves us some time and money trying to locate the thing. The guy tells my spouse that we need to put a sheet of plywood over it or something to keep someone larger than we are (read: my brother) from accidentally falling in.
Then, they open it up. Horrors. We've tried to protect the innocent, considering what you're looking at.
Turns out that our tank is probably an old Sears model from the 1950s, iron, about 500-600 gallons. It's been retrofitted, probably by the previous owner. Super. The guy tells us that if he was inspecting our property, and saw this setup, he would have never given it a pass. Good to know. Three years later.
(You can tell that this whole episode doesn't bother me at all. $12,000 or suffer toilet trauma like never before doesn't bug me at all.)
Anyway, the guy pumps it.
Nice and "clean." At this point in time he thinks that we could probably last on the system a couple more years.
Then he tests our leach field. Turns out it doesn't really leach. At all. For $500 cash (it usually costs $800-$1,000) he'll come out and try to make it drain better. No guarantees that it will work, of course. At this point, there's really not much more to do but seal the thing up.
After he leaves, my spouse calls the utility district. They confirm the prices, and then say that we can actually do all the work ourselves to save us that $5,000. But, we'll have to sign a waiver that we'll be liable and pay for any problems in the line "downstream" of us ourselves. I don't know about you, but that sounds like an awful lot of liability to me. So I'm not so comfortable with that, either, even though it saves us money. We could dig the trench ourselves, and have a contractor could lay the line and do the attachment. We'll have to price that out and see how it goes.
We should even be able to decommission it ourselves. That will involve getting an inspector over here, who will watch us get it pumped, break the bottom out with an iron tamping bar, and then fill it with sand. Then I might dance on top of it and light my money on fire, you know, just for fun.
At any rate, we need to do something. This isn't a problem that will just go away or solve itself. But we won't worry about it right now. My brother moves in with us this weekend. We'll just have to let him know to go easy on the tp.
Sunday, August 24, 2008
Clay Play
Strap yourself in for a long post. When we don't post often, it means we're getting a lot done! At least that's what we tell ourselves. Sorry you haven't heard from us in a little while.
We finished the ceiling a couple of weeks ago, Solatubes and all. The Solatube dampers are in, and so we can let less light in, should we so choose.
As of right now, our walls are very close to being finished. We've nearly completed the application process of the clay, which has been fairly easy to work with, overall. We're liking the way it looks, and we think we'll be able to do a better job next time.
How it works is you put the sanded primer on, mix up the first coat (coarse grit, which is called Loma), trowel that on to the walls, let it dry, and then mix up and put on the second coat (which you can either do another Loma coat or use the fine grit, Porcelina). We used the Porcelina because we wanted a smooth finish. Then you do what's called burnishing, where you're basically compressing the clay to harden it, but also to smooth it out further and get the finer particles to the top.
We've put on our Loma coat and the Porcelina coat, and we've burnished two of the walls. It has taken a LOT longer than we thought it would, but working every night after work and on the weekends, we're nearly finished. What hasn't taken a lot longer than we thought it would, though?
Here's how our process went.
We put the Loma into the bucket, and using a drill we got off of craigslist for the express purpose of mixing stuff, added the water and tried to mix it.
Unfortunately, we couldn't get the water to distribute through the Loma powder well enough to actually USE the mixer. So, we started it off the old fashioned way:
Hand mixing worked out surprisingly well. Good thing I keep my fingernails super-short, or I would have been picking Loma out for weeks. Anyway, once we got all the Loma more or less wet, we were able to use the drill mixer without it smoking.
Then it was time to add the color. We chose Tucson Gold (yellow), and so we mixed up the pigment paste and added to the Loma. I was worried that the pigments wouldn't come out of our clothes, but they did. The clay has come out of our clothes each time (it's just dirt), and the pigment hasn't left any stains.
The thing about the pigment is that each batch is different, so you have to make a big enough batch so that you have some left over, because it's almost certain that you won't have the same color next time. (Gotta account for natural variation in color.) The Loma mixed up very nicely, in the end, about the consistency of pudding.
Then it was time to apply the Loma. All said and done, it took between eight and 10 hours to do the Loma coat.
And here's how the room looked with the Loma coat.
Then we mixed up the Porcelina. This time we followed the directions to the letter to try and avoid the problems we had with the Loma, but the hand mixing actually worked better. Oh well. In order to apply the Porcelina, we wetted down the layer of Loma on the walls with a spray bottle, and then applied the Porcelina right on top. The Porcelina was much smoother than the Loma, and was the same earthy yellow color (which incidentally matches our pendant lights perfectly).
And now we're burnishing!
We're very, very happy with the color and the way the room looks, and we're really excited to get the burnishing done, which will happen this week, and then begin the bookshelf and trim, which we'll do after moving my brother in next weekend.
Our permit runs out next month (gasp, gasp), and so we need to really get cracking. We also have to put on and paint siding, so we mocked up a couple of different widths. We ended up going with the width on the right (five inch exposure) because it's not a special order item. Now we just have to make our order and we'll install that soon. Whew!
We finished the ceiling a couple of weeks ago, Solatubes and all. The Solatube dampers are in, and so we can let less light in, should we so choose.
As of right now, our walls are very close to being finished. We've nearly completed the application process of the clay, which has been fairly easy to work with, overall. We're liking the way it looks, and we think we'll be able to do a better job next time.
How it works is you put the sanded primer on, mix up the first coat (coarse grit, which is called Loma), trowel that on to the walls, let it dry, and then mix up and put on the second coat (which you can either do another Loma coat or use the fine grit, Porcelina). We used the Porcelina because we wanted a smooth finish. Then you do what's called burnishing, where you're basically compressing the clay to harden it, but also to smooth it out further and get the finer particles to the top.
We've put on our Loma coat and the Porcelina coat, and we've burnished two of the walls. It has taken a LOT longer than we thought it would, but working every night after work and on the weekends, we're nearly finished. What hasn't taken a lot longer than we thought it would, though?
Here's how our process went.
We put the Loma into the bucket, and using a drill we got off of craigslist for the express purpose of mixing stuff, added the water and tried to mix it.
Unfortunately, we couldn't get the water to distribute through the Loma powder well enough to actually USE the mixer. So, we started it off the old fashioned way:
Hand mixing worked out surprisingly well. Good thing I keep my fingernails super-short, or I would have been picking Loma out for weeks. Anyway, once we got all the Loma more or less wet, we were able to use the drill mixer without it smoking.
Then it was time to add the color. We chose Tucson Gold (yellow), and so we mixed up the pigment paste and added to the Loma. I was worried that the pigments wouldn't come out of our clothes, but they did. The clay has come out of our clothes each time (it's just dirt), and the pigment hasn't left any stains.
The thing about the pigment is that each batch is different, so you have to make a big enough batch so that you have some left over, because it's almost certain that you won't have the same color next time. (Gotta account for natural variation in color.) The Loma mixed up very nicely, in the end, about the consistency of pudding.
Then it was time to apply the Loma. All said and done, it took between eight and 10 hours to do the Loma coat.
And here's how the room looked with the Loma coat.
Then we mixed up the Porcelina. This time we followed the directions to the letter to try and avoid the problems we had with the Loma, but the hand mixing actually worked better. Oh well. In order to apply the Porcelina, we wetted down the layer of Loma on the walls with a spray bottle, and then applied the Porcelina right on top. The Porcelina was much smoother than the Loma, and was the same earthy yellow color (which incidentally matches our pendant lights perfectly).
And now we're burnishing!
We're very, very happy with the color and the way the room looks, and we're really excited to get the burnishing done, which will happen this week, and then begin the bookshelf and trim, which we'll do after moving my brother in next weekend.
Our permit runs out next month (gasp, gasp), and so we need to really get cracking. We also have to put on and paint siding, so we mocked up a couple of different widths. We ended up going with the width on the right (five inch exposure) because it's not a special order item. Now we just have to make our order and we'll install that soon. Whew!
Subscribe to:
Posts (Atom)